Cash Budgeting

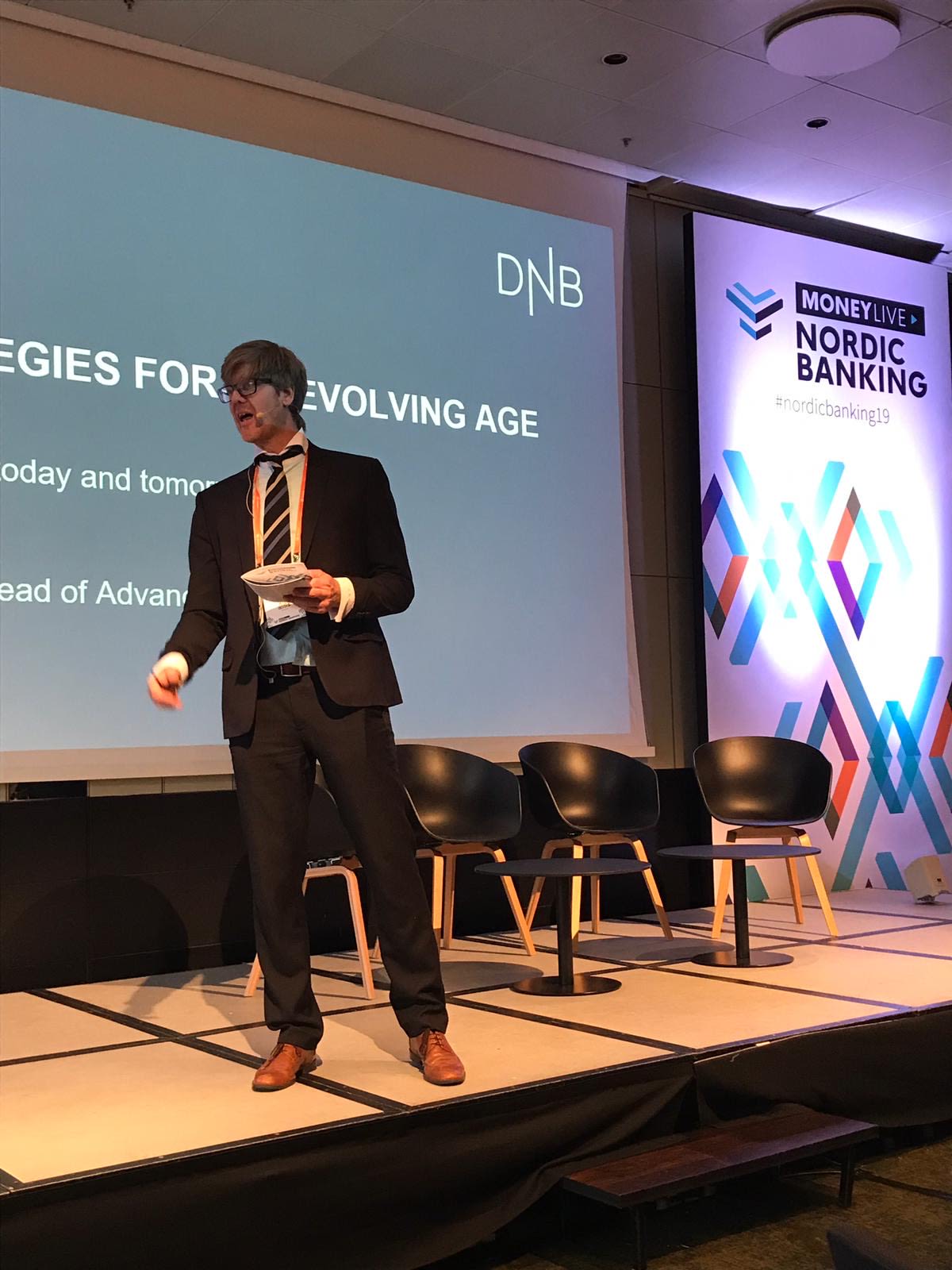
This short training lesson will guide you through the techniques of cash budgeting
We will use a short example, which is the company "Nordgaards Industries". We will budget the company for 2021.
The intention is to create an understanding for the process of production in a company (the Supply chain). Based on this understanding, we will go through the cash budgeting techniques.
We will begin with a FY budget!
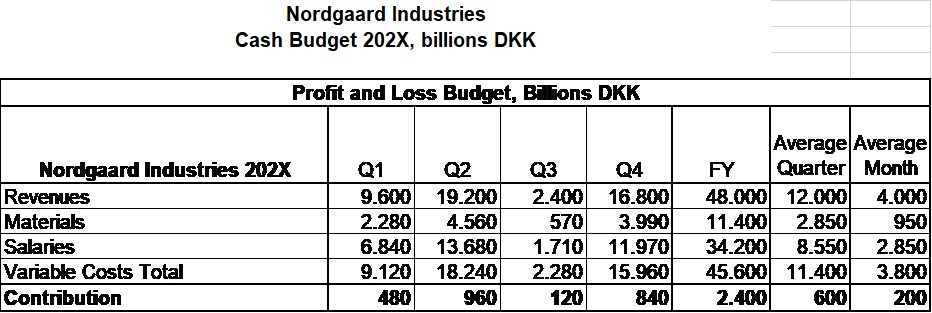
Secondly, - we need the assumptions for budgeting for 202X
Assumptions for the cash budget:
The company is started on the first of january 202X. Therefore, there are no assets on the first day.
- Customers buying products will be given 4 months of credit
- Inventory of finished goods should cover 2 months of activity
- Work in progress is not very high, it only covers half a month (15 days) of production
- Inventory of materials should cover 1.5 month of production
- The suppliers of materials offers 1 month of credit
Now, let us first understand - why does a company need an inventory of finished goods?
To be absolute sure to be able to supply goods for the customer, at any time, - the company needs an inventory of finished goods. Another reason for having an inventory of finished goods is production capacity.
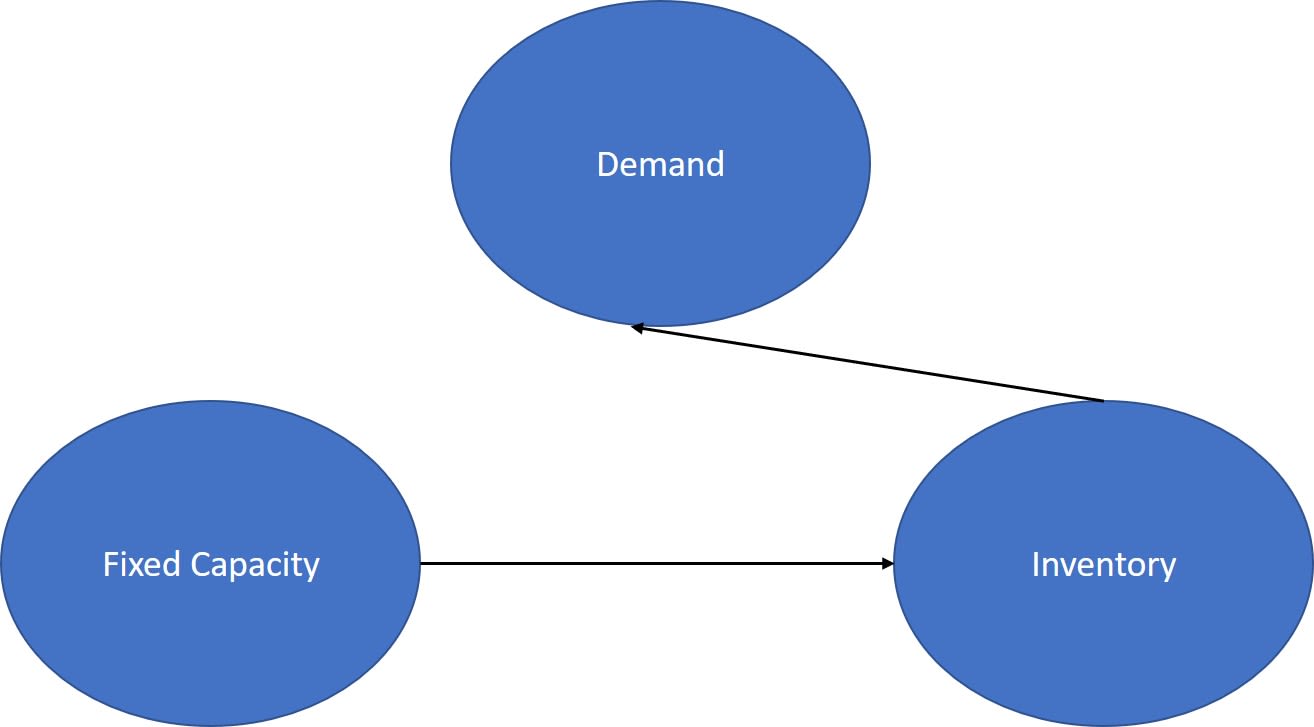
A company is able to produce 2.000 products every half year. The demand for products first half of the year is 1.500 products and 2.500 products in the second half year. It is easy to see that the company would manage this by producing 2.000 every half year and having an inventory of + 500 as the beginning of second half year
Accounts Receivables
On the first of January, there are no accounts receivables. The company is completely new. As the year elapses, sales creates accounts receivables. The assumption for accounts receivables is that the company offers the customer an average credit of 2 months. So let us look at the budget for the Profit and Loss Statement
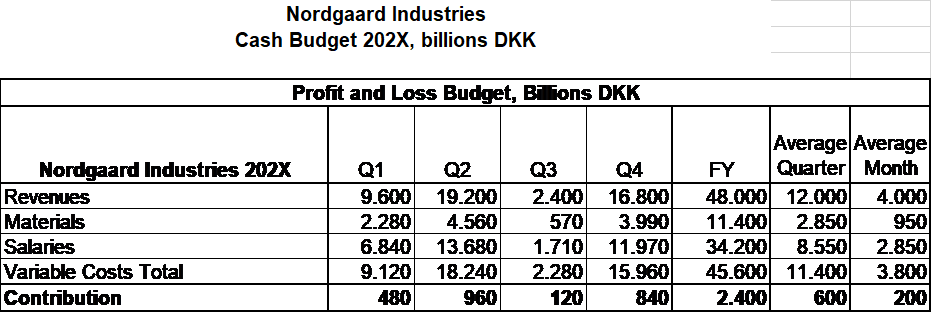
You can see that the average monthly sale is 4.000. Remember that this is the first assumption that we have taken, that the sale is actually exactly the same level, every month.
If customers are given four months of credit, the at the end of the year, the customers who bought products in december, november, october and september will not have paid for their products yet. We are also assuming that all customers are paying in accordance to the payment terms. No one pays too early and no one pays to late. So, very easy! The turnaround for accounts receivables is 12/4 = 3 times a year. The Accounts receivables will thus be 48.000/3 or 48.000/12*4. It is 16.000
Inventory of Finished goods
The inventory of finished goods are set out to cover two months of sale. Again, in this case the sale is exactly the same every month. So finished goods inventory should a total amount of products at a sales price of 8.000 (2 times 4.000)
Now, - the cost of a product on inventory is the cost price and we thus need to calculate the difference between the sales price and the cost price.
The company sells products for 4.000 a month and the cost of producing the products are 3.800. So the value of the inventory will be 7.600, as the contribution margin is only 5%. The cost price of products to be sold for 8.000 is thus 8.000 * (1-0.5) = 7.600
Total Production of finished goods
We remember that as we started the company on the first day of january 202X, there are no finished goods on the inventory as we start the year. At the end of the year we intend to have two months of finished products sale on the inventory. During the year we thus have to produce all the products that are to be sold and on top of that products for the inventory.
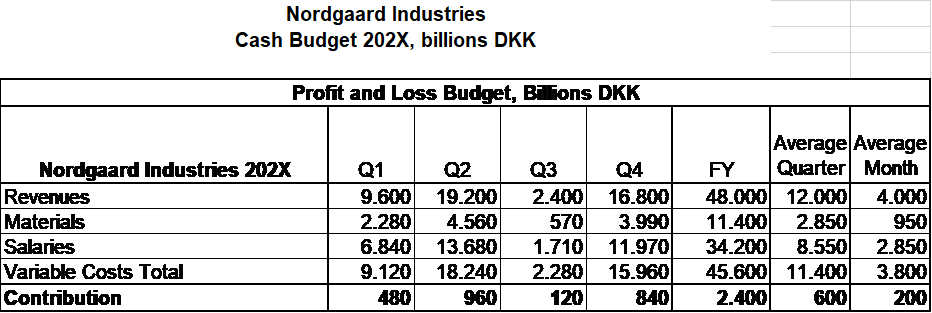
The total sale is 48.000 with production costs of 45.600 and on top of it, the value of the inventory of finished goods, which was 7.600. Our total cost of production is thus (45.600 + 7.600) = 53.200. This is the value of finished goods.
Work in progress
The reason for having work in progress is the production time. If the production time of a product is say 48 days, then on the last day of December there will be products that begun to be produced on the 31th of December at say 00.01. They will finish on the 1th of January at 23.59. On the 31th of December at 23.59, they will thus be half way through the production.
You will discover along the way that we are making a number of assumptions. One of them is that costs are applied at the same rate throughout the production. Therefore, if the production is 25% finished, it holds 25% of the production costs etc. We also assume (in this case) that both salary and materials are applied at the same pace. In real life we will have to evaluate the importance of these assumptions and whether to increase the level of detail in our budgeting.
In our example the work in progress should cover half a month of production of finished goods. The production of finished goods is 53.200. The value of work in progress is thus 53.200/24 = 2.217
Total cost value of total production
We now know that we are producing a value of 53.200 in finished goods and 2.217 in work in progress. The total cost value of production is 55.417
How much of the total cost value are materials?
In our P/L budget we see that the production costs are 45.600 of which materials are 11.400 so 11.400/45.600 is 25%. Materials are thus 13.854 of the 55.417 which is the value of total production.
Inventory of Materials
Inventory of materials should cover 1.5 months of the use of materials in the total production. This is thus 13.854/12*8 = 1.732
Total purchase of Materials
We know that the value of the total production is 55.417, of which materials are 13.854 (25%) and as the inventory of materials is 1.732, then the total purchase of materials are (13.854+1.732) = 15.586
Accounts Payables - Vendor Credit
Our supplier is offering us a 1 month credit. As the total purchasing of materials is 15.586, the supplier credit will be 15.586/12*1 = 1.299
The Complete Overview
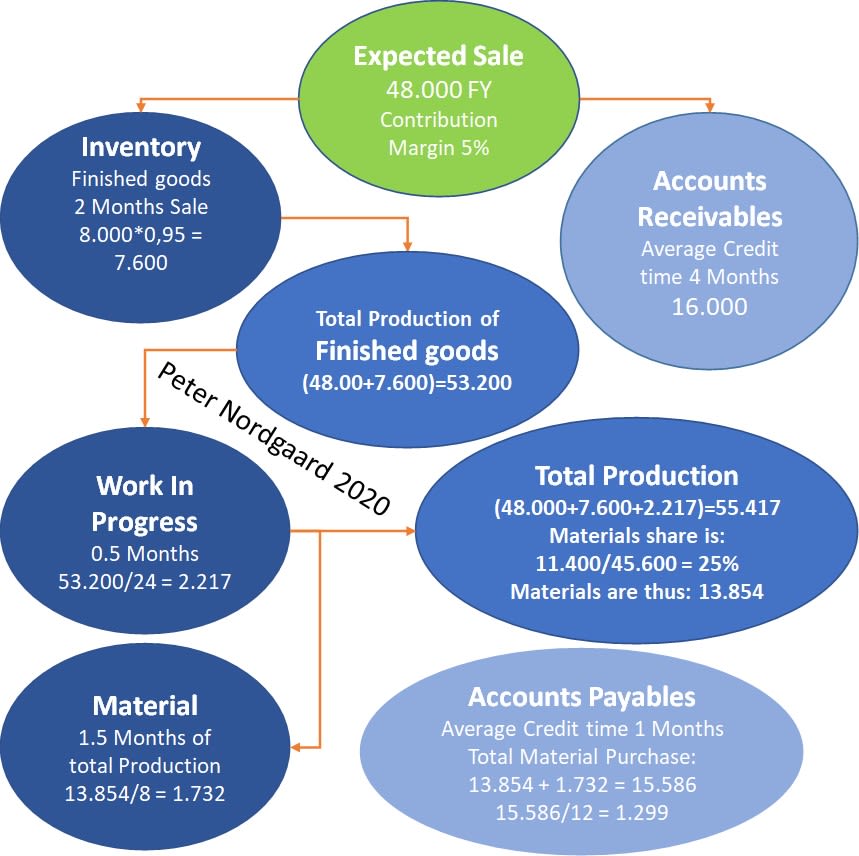